The company that makes tracks for most of Britain’s armoured vehicles and those of other allied nations worldwide has reverse-engineered old Soviet designs from tank parts and documents held in museums to keep Ukraine’s army going.
The world’s largest tank museum has been providing parts from vehicles held in their collection and original Soviet documentation from their archives to a historic British family-owned engineering firm to produce new stores of spares for vintage Russian tanks serving on the front line for the Ukrainian armed forces, a report reveals. The Bovington Tank Museum in Dorset, England which holds hundreds of vehicles including the world’s first working tank has a collection which mainly focuses on vehicles that had been operated by Britain’s armed forces, or which have been captured by British soldiers in combat, has a large selection of Soviet-era tanks.
The Ukraine War, particularly as the frontline became more static through the winter of 2022-23 has heavily featured mine warfare and this has meant a large number of Ukrainian tanks taken out of service that could still fight except for having had their rotating caterpillar-type tracks blast-damaged. The deal suggests Ukraine’s intense war of self-defence is taking its military equipment beyond whatever Soviet-era stores and spares were left in the country at the end of the Cold War.
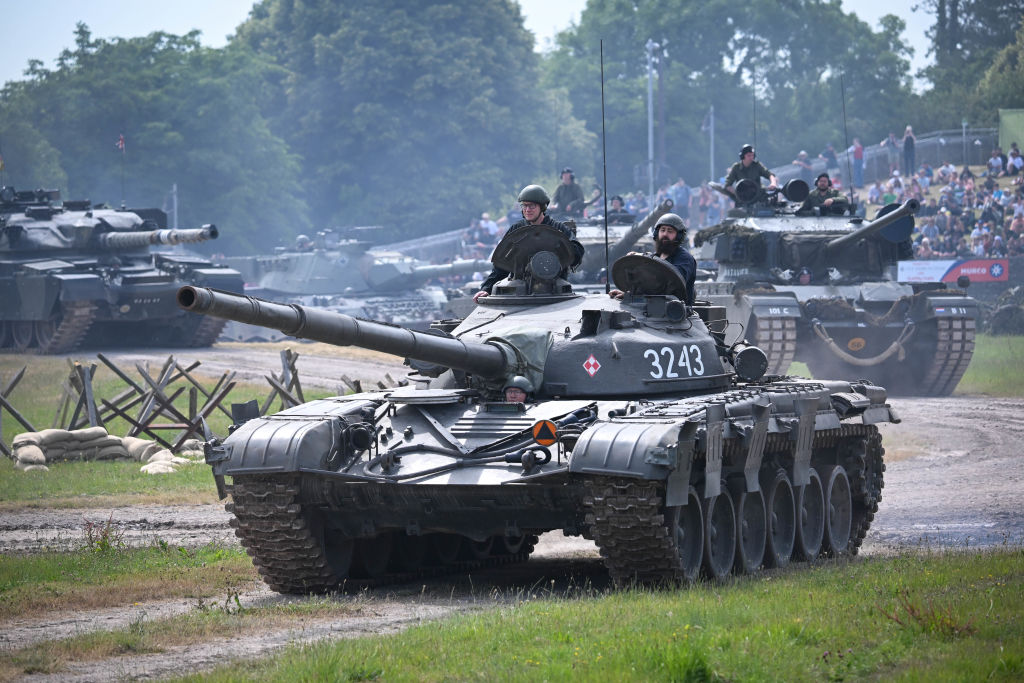
BOVINGTON, ENGLAND – JUNE 23: Soviet Cold War era Main Battle Tank. The T-72 is seen at TANKFEST, on June 23, 2023 in Bovington, England. Bovington The Tank Museum holds the world’s largest collection of tanks, covering the period from the First World War to the present day. TANKFEST is a three day event featuring the world’s biggest live display of historic armour. (Photo by Finnbarr Webster/Getty Images)
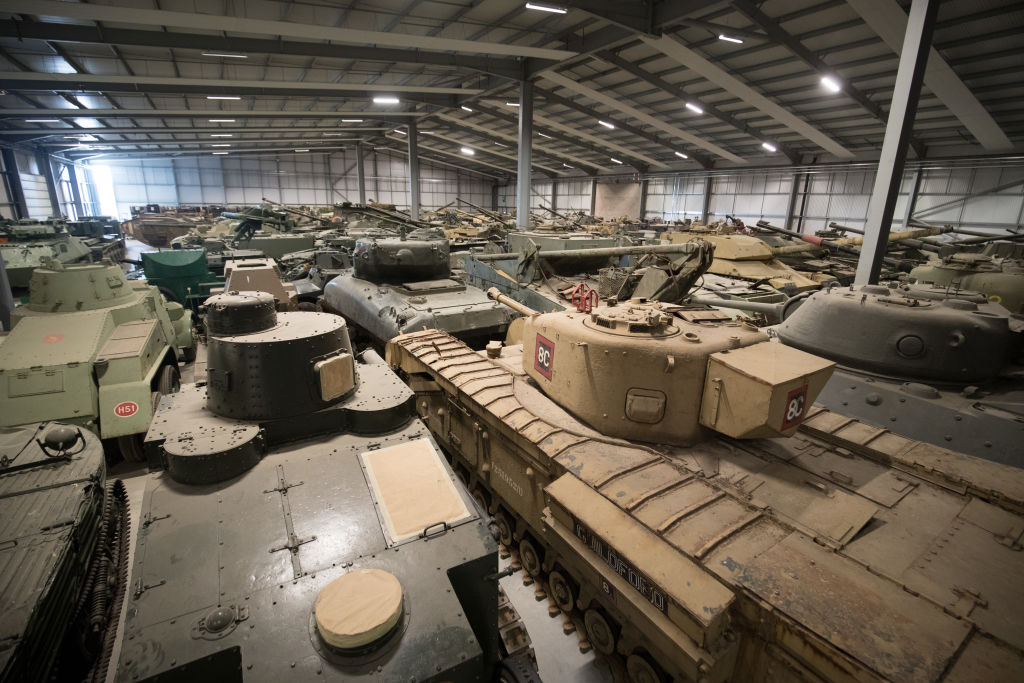
BOVINGTON, DORSET – SEPTEMBER 13: Tanks stored at the Vehicle Conservation Centre at the Bovington Tank Museum are displayed ahead of this weekend’s Tiger Day, which will feature a Tiger tank, the only working example in the world, being demonstrated to the public, on September 13, 2017 in Dorset, England. Bovington The Tank Museum is home to Tiger 131, which was captured intact by the allies during fierce fighting in the Tunisian desert in 1943 and is currently part of a world-first exhibition, The Tiger Collection, which showcases the entire Tiger family side-by-side. Such was the importance of its capture that Prime Minister Winston Churchill and King George VI went to North Africa be pictured with it. (Photo by Matt Cardy/Getty Images)
That Cook Defence Systems of County Durham, England would be producing tank tracks for Soviet-made vehicles was quietly floated last year, as the Chief of the General Staff, General Sir Patrick Sanders visited the business in June and discussed how the company is “supporting armoured vehicles in service in Ukraine”.
Cook, which exports tracks to Europe, the Middle East, South East Asia and Australia was “commissioned” by the British government to start work on making spares for Soviet tanks last year and signed a multi-million-pound contract for the components and for spare tracks for the British-made armoured vehicles which have been donated to Ukraine in February 2024. The Ministry of Defence said then the deal would “provide hundreds of spare caterpillar tracks for tanks and armoured vehicles – which will allow the AFU [Armed Forces of Ukraine] to recover and restore vehicles damaged by anti-tank weapons and landmines… The company’s experts have been examining and analysing Soviet-era vehicles, some salvaged from Ukraine, to create new tracks to fit a range of requirements.”
It was reported by the UK Defence Journal that the deal would cover tracks to supply 500 Ukrainian armoured vehicles. Among those Soviet vehicles in use defending Ukraine which Cook is making new parts for are the venerable 1950s-era lightweight armoured amphibious MT-LB, the 1960s-era BMP infantry fighting vehicle, and the 1970s-era T-72 Main Battle Tank.
As stated by the Daily Telegraph, creating tracks for these vintage vehicles has not been straightforward and has involved detailed study of original parts and documentation. The report notes the Bovington Museum was quick to assist, with curator David Willey saying: “in some cases the people from the Cold War era are no longer around and knowledge has been lost. Details such as the angles, pitch and tension required for the new tracks were sought and our archive was able to provide them with old manuals and blueprints for the tanks.
“We also found examples of the actual items required such as T-72 tracks and pins from one of the vehicles in the collection. The new parts could then be made accurately in the UK.”
William Cook, the director of Cook Defence Systems said of his company’s involvement: “delivering these contracts for Ukraine has been a very different challenge. We have had to reverse-engineer Soviet-era equipment using limited reference material and a lot of our own know-how, while working with the manufacturing processes and materials available to us rather than the original Russian ones. We are doing all this with an urgency unknown in peacetime. We know there are Ukrainian soldiers on the frontline whose lives depend on what we do.
“One of the biggest challenges has been almost doubling our output. We have reconfigured production lines and recruited new people wherever possible. Everyone is working exceptionally hard, but we are incredibly proud to be making a difference.”
COMMENTS
Please let us know if you're having issues with commenting.